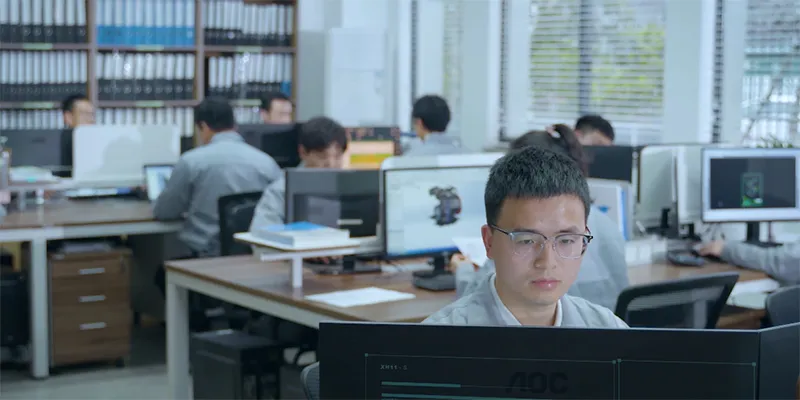
Our team provides 24/7 assistance to address technical inquiries. Remote support is available within two hours, and if on-site service is required, technicians can be dispatched within 24 to 48 hours.
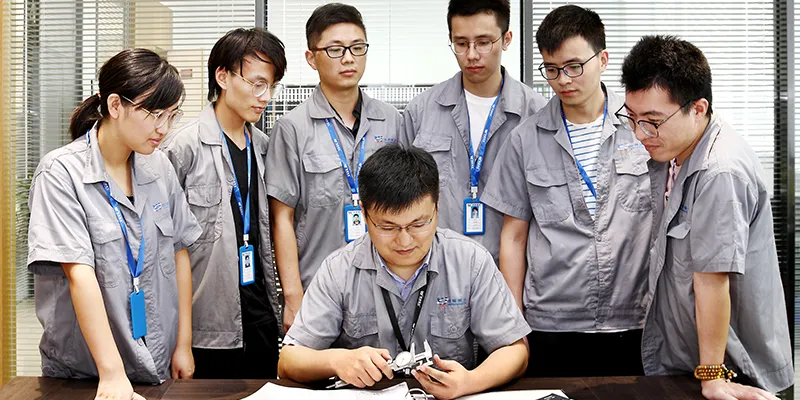
We offer custom manufacturing based on client specifications, including the option to visit facilities for on-site measurements. Tailored magnetic separation solutions are designed to meet specific processing needs.
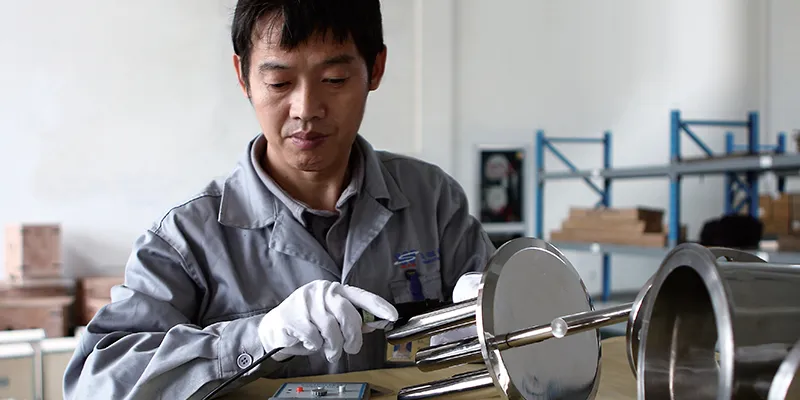
Before shipment, every product undergoes rigorous testing for performance, appearance, material quality, and processing standards. A detailed inspection report is provided. We also assist customers in verifying magnetic strength remotely or by analyzing mailed-in samples, offering recommendations for replacements when necessary.
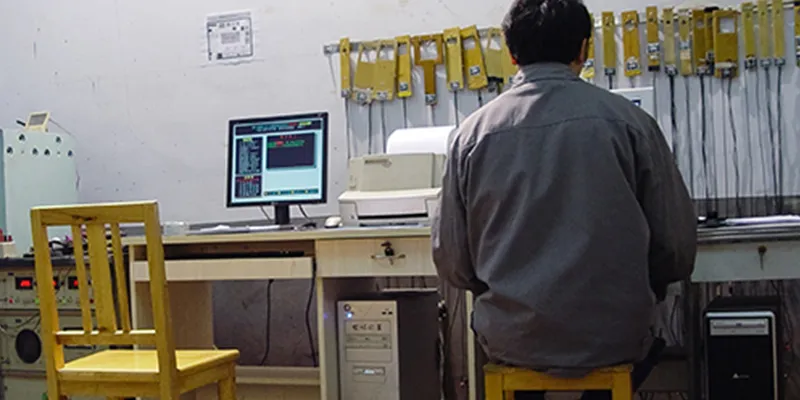
A warranty period of 12 months from installation or 18 months from delivery, whichever comes first, is provided when purchasing any of our magnetic separation equipment. Any defects resulting from design, manufacturing, or assembly issues will be addressed at no additional cost.
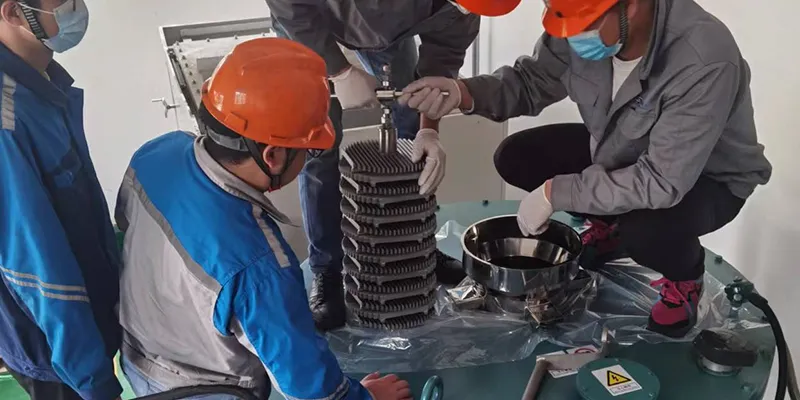
For problems that cannot be resolved remotely, our technicians are dispatched promptly to carry out on-site repairs and maintenance. Spare parts and replacement components are available at competitive prices to ensure uninterrupted operation.
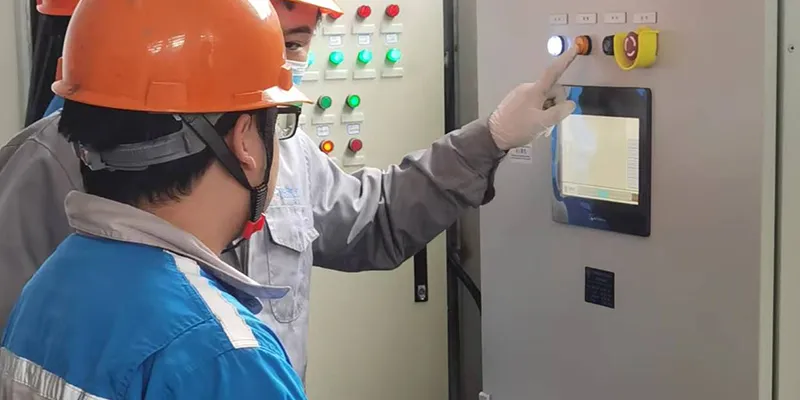
For production line upgrades, our team conducts on-site assessments to analyze existing setups, identify inefficiencies, and determine key areas for improvement. We work closely with customers to understand specific challenges and provide tailored solutions that enhance performance, improve energy efficiency, and extend equipment lifespan. Our goal is to optimize operations while ensuring a cost-effective and seamless transition to upgraded systems.
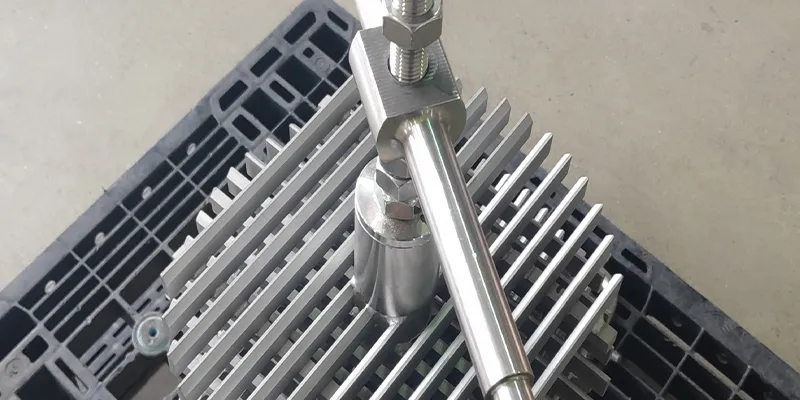
We maintain an inventory of spare parts for standard models to ensure quick replacements when needed. Support and compatible components for third-party brands are also available upon request.