Our comprehensive magnetic separation solutions are widely adopted across multiple industries, including lithium battery manufacturing, chemical processing, food production, and pharmaceuticals. Various renowned companies rely on our expertise to enhance material purity, improve product quality, and optimize production efficiency.
We have established long-term collaborations with many well-known brands, including:
- Lithium Batteries: BYD, CATL, EVE Energy, CALB, Penghui Energy, Gotion High-Tech
- Battery Materials: Huayou Cobalt, CNGR Advanced Materials, GEM, Shanshan, BTR, Wanrun New Energy, Rongbai Technology, Defang Nano, Enjie, Capchem
- Food Processing: Orion, Nestlé, Wahaha, COFCO, Yihai Kerry, Xu Fuji
- Chemical Industry: Rianlon, Cangzhou Mingzhu, BASF, Formosa Plastics, DuPont, Kingfa Sci & Tech
- Pharmaceuticals: Huakang Pharmaceutical, WuXi AppTec, Zhejiang Pharmaceutical
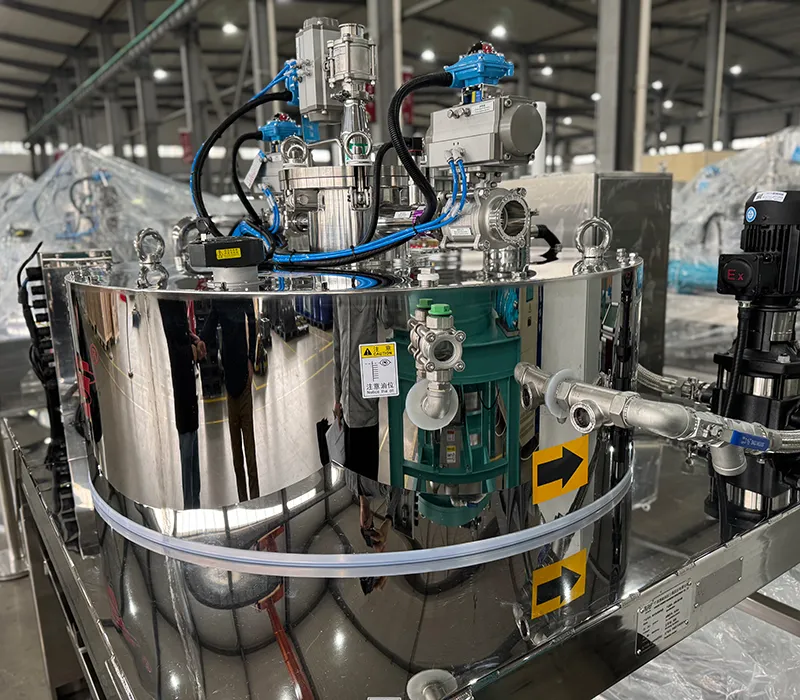
A chemical material manufacturer sought a solution to reduce ferrous contaminants in PVDF powder production, with a target impurity level below 50 ppb. To meet these strict quality standards, we provided two EMS-250-D6 high-performance electromagnetic separators with 250mm inlets, ensuring high-efficiency ferrous metals separation. Additionally, spare screen assemblies were supplied for quick replacements, minimizing downtime and maintaining continuous production. Our expertise in magnetic separation enables manufacturers to achieve superior product purity and meet stringent industry standards, reinforcing our commitment to high-quality industrial solutions.
Related Products
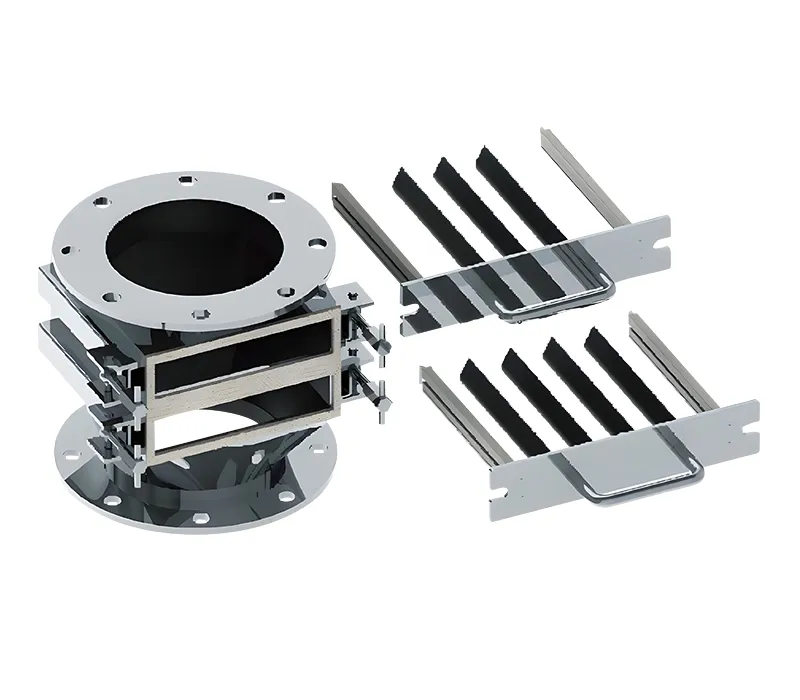
A pharmaceutical company specializing in creatine powder production required a solution to remove fine ferrous contaminants during processing. The separation system needed to be integrated into the pipeline and operate under normal pressure conditions to ensure a smooth production flow without disruption.
To meet these requirements, we provided a two-layer drawer magnetic separator with a 200mm inlet diameter and 12000GS magnetic bars arranged in a 3+4 configuration. This setup ensures effective iron removal while maintaining material integrity and process efficiency.
Related Products
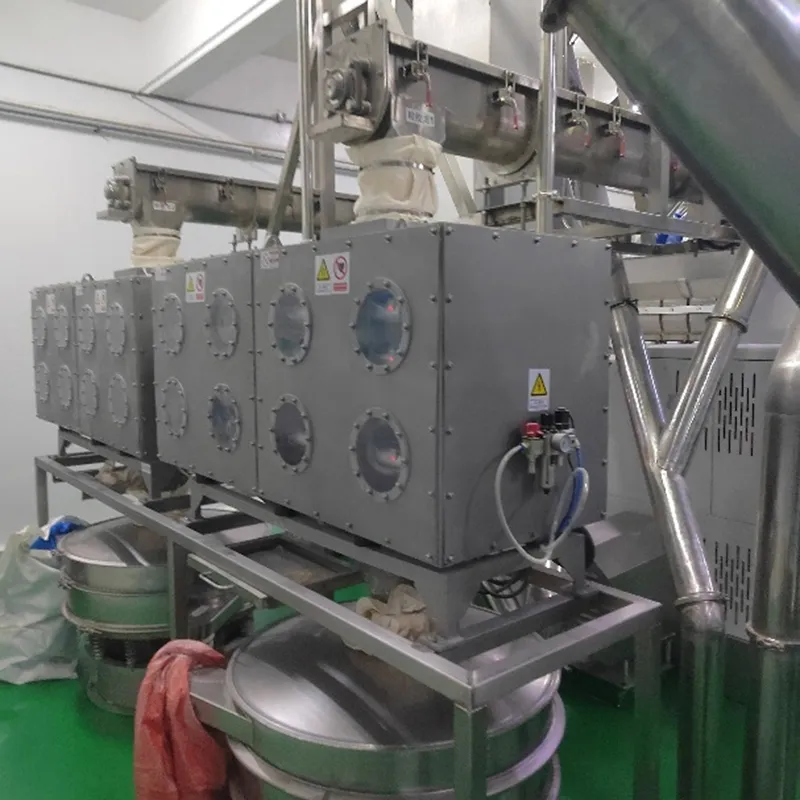
A food processing company specializing in potato starch production needed an efficient way to remove ferrous contaminants introduced during grinding. With a processing capacity of 2 tons per hour, the system had to operate under normal pressure conditions while maintaining continuous production without manual cleaning interruptions.
To address these requirements, we provided two automatic powder magnetic separators: one with a 200mm inlet diameter and another with a 150mm inlet diameter, both designed with six-layer magnetic grids. Featuring 12000GS magnetic bars and PLC-controlled automation, these systems allow for continuous in-line separation and self-cleaning, ensuring effective impurity removal while keeping production efficient and uninterrupted.
Related Products
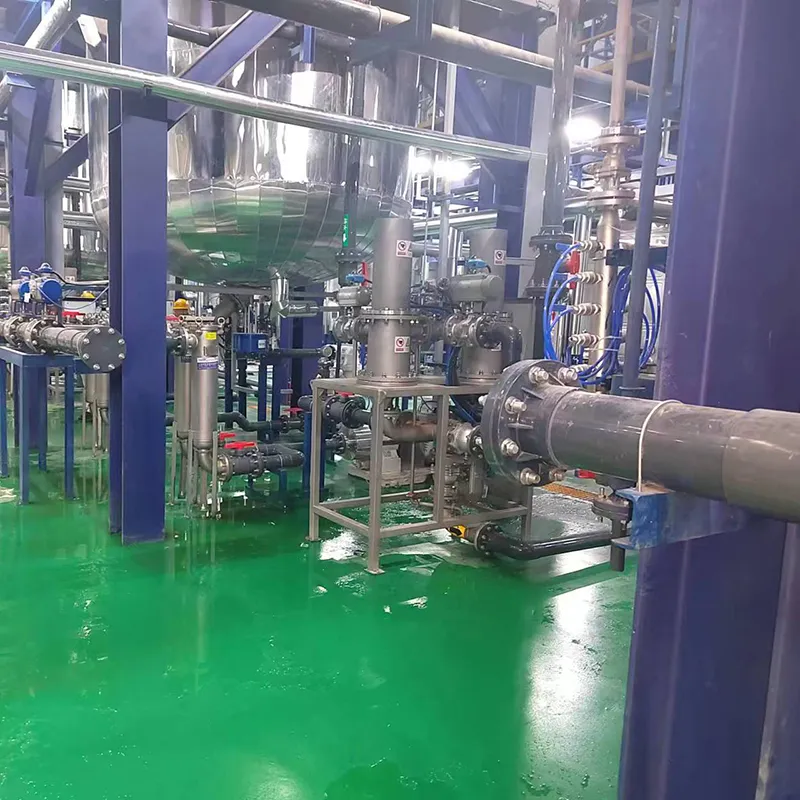
A manufacturer specializing in lithium iron phosphate (LFP) slurry required a solution to remove ferrous contaminants originating from raw materials and pipeline transport. With a processing capacity of at least 15m³ per hour and an operating pressure below 0.6MPa, the system needed to ensure efficient separation while integrating seamlessly into the existing production process.
To address these needs, we supplied a 65mm dual-barrel automatic slurry magnetic separator with a magnetic strength of 10,000GS. Designed for automated impurity removal, the system was connected to the DCS (Distributed Control System), allowing for remote monitoring and self-cleaning operations, reducing manual intervention and improving overall efficiency.
Related Products
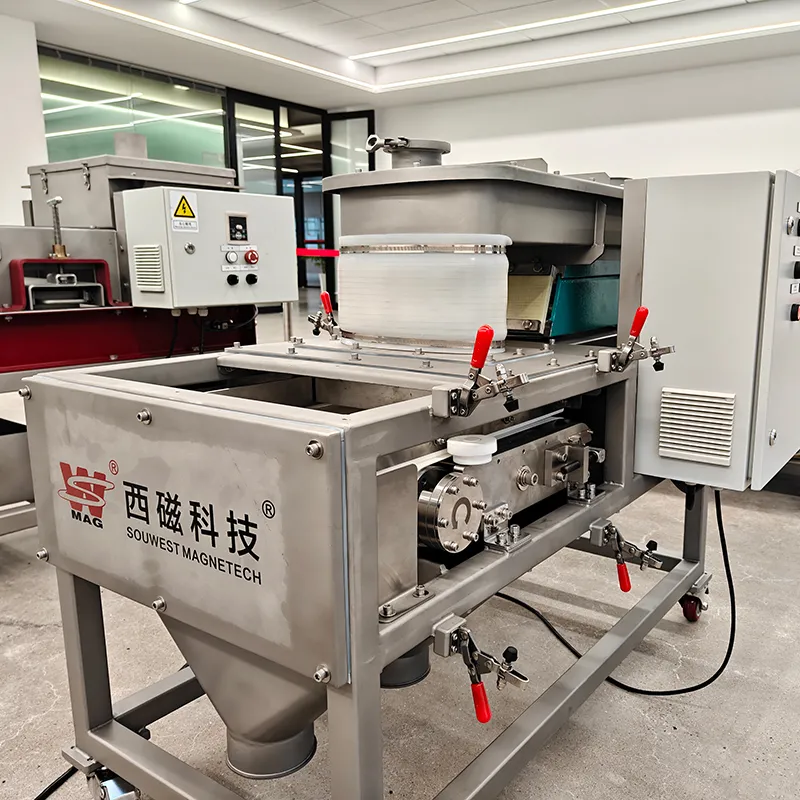
For this case, a plastic manufacturer processing polyamide pellets and partial powder materials required a solution to remove ferrous contaminants introduced from raw materials and equipment wear. With a processing capacity of at least 5m³ per hour and operation under normal pressure conditions, the magnetic separation system needed to ensure continuous impurity removal without material loss.
To meet these requirements, we provided a 600mm dual-layer cross belt magnetic separator with a magnetic roller strength of 15,000GS. The fully enclosed filtration area prevents material leakage while allowing for automated separation, ensuring effective impurity removal throughout the process.
Related Products
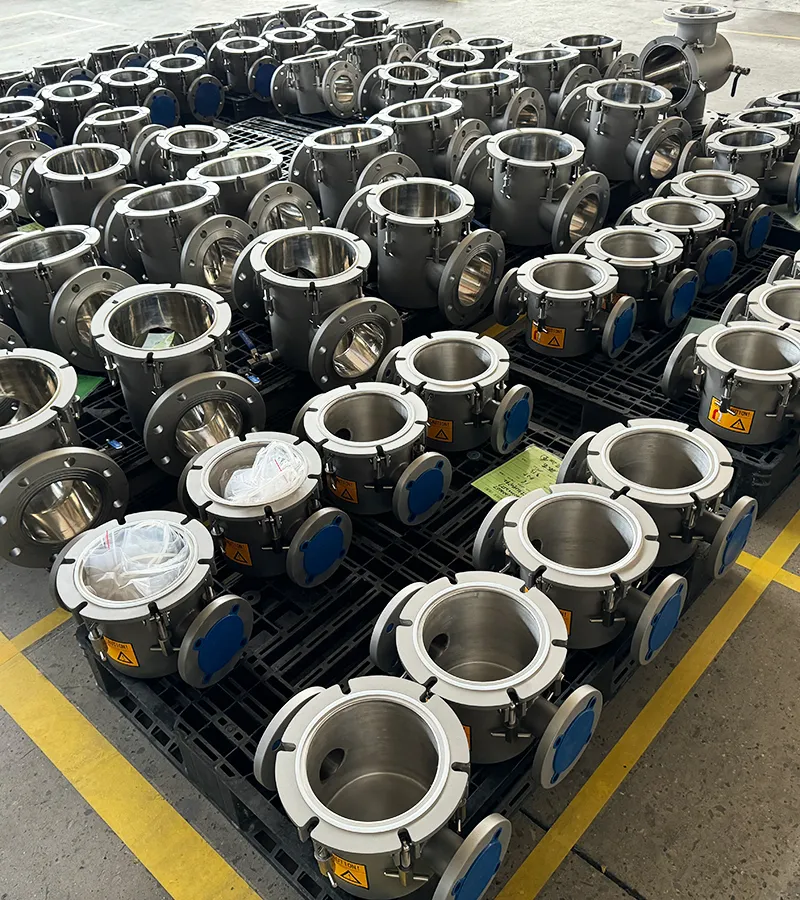
A lithium battery manufacturer specializing in lithium iron phosphate (LFP) slurry required a solution to remove ferrous contaminants introduced from raw materials and material transport. With a flow rate ranging from 35 to 110m³ per hour and slurry temperatures between 70-90°C, the system needed to maintain effective separation while operating under high-temperature conditions. Additionally, given the mildly corrosive nature of LFP slurry, durability and material compatibility were key considerations.
To address these requirements, we supplied 112 pipeline magnetic separators of varying diameters (200mm, 150mm, etc.) equipped with 12,000GS magnetic bars. These separators were specifically designed for temperature resistance up to 120°C, with 316L stainless steel flow components to ensure long-term stability and corrosion resistance. This setup allows for consistent impurity removal, helping maintain the purity of LFP slurry while ensuring seamless integration into the production process.
Related Products